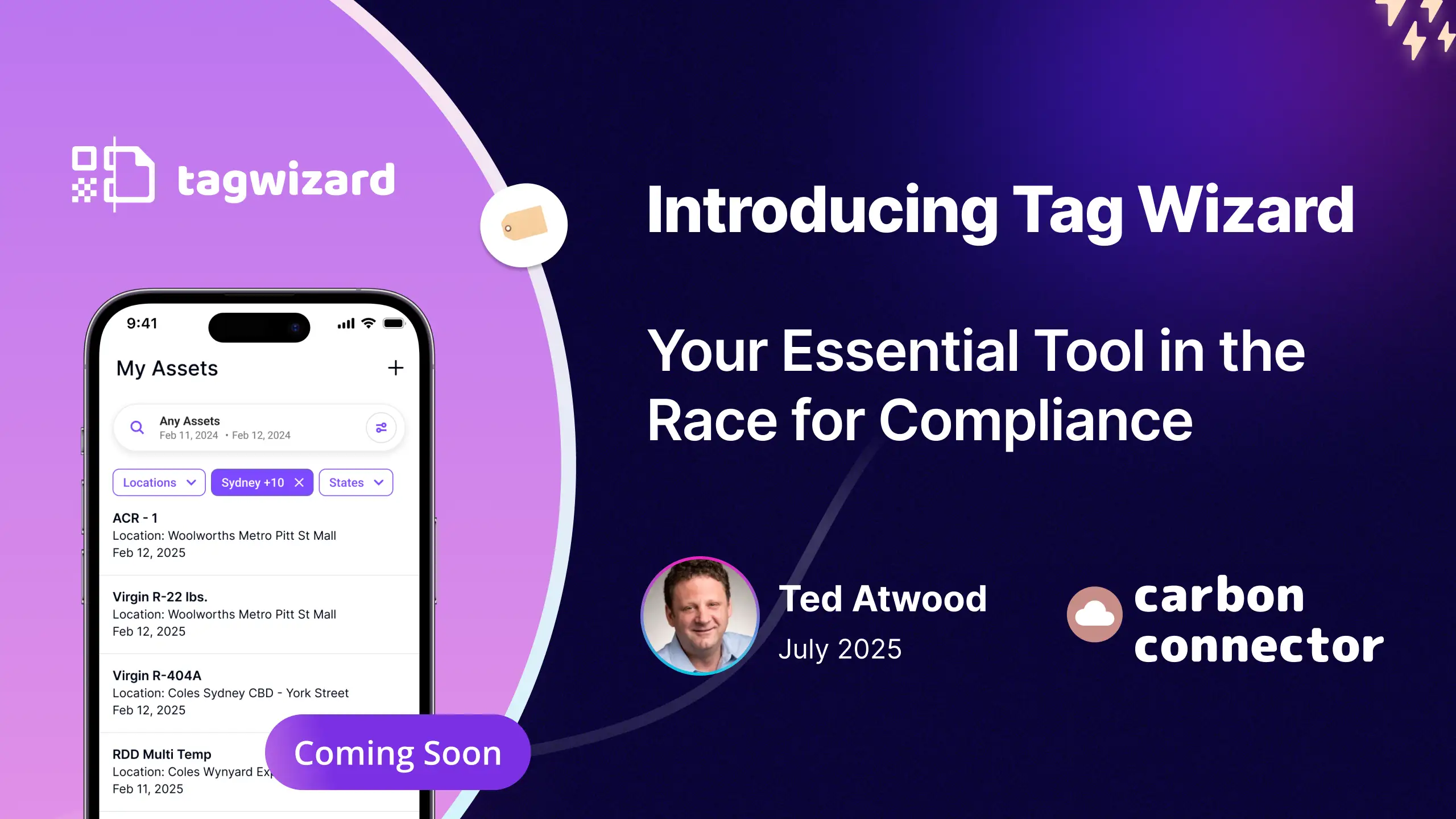
Introducing Tag Wizard: Your Essential Tool in the Race for Compliance
Table of Contents
ToggleOur Shared Mission: Keeping Things Simple, Compliant, and Optimized with Tag Wizard
Tag Wizard is designed to close those administrative gaps, turn your due diligence into a competitive advantage, and ensure you’re not just running the race, but winning it.
It streamlines compliance and asset management processes, making it easier to maintain accurate records and meet regulatory requirements. In an era where every label is a legal document, and every data point can trigger an audit,
Tag Wizard is the essential tool for mastering the new skills of refrigerant lifecycle management.
The benefit of using Tag Wizard is clear: improved operational efficiency, reduced risk of non-compliance, and greater confidence in your asset tracking and compliance efforts.
Tag Wizard also helps maximize your return on investment by improving asset utilization and providing detailed reporting and visualization for better performance analysis.
Tag Wizard supports compliance and asset management needs across various industries, including retail, healthcare, and manufacturing.
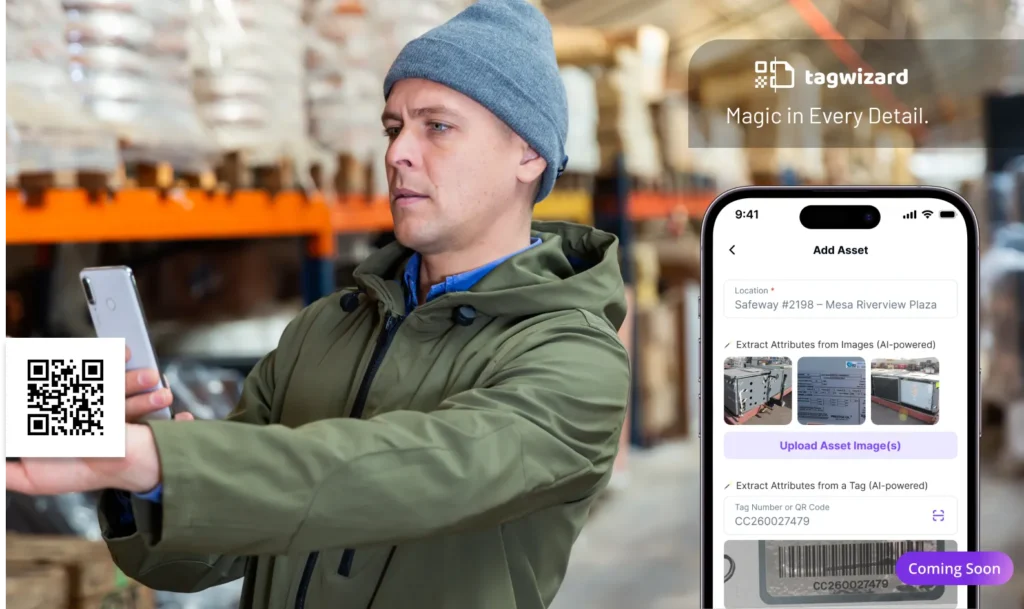
What is Asset Tagging?
🏷️ Asset tagging is the process of assigning a unique identifier
such as a barcode, QR code, or serial number, to each asset a company owns, and asset labels are crucial in this process.
Tag Wizard is specifically designed for Key HVAC/R assets.
Effective asset tagging is a cornerstone of modern asset management.
Selecting the appropriate asset tag for each asset is crucial, taking into account durability, identification, and security features, as well as using proper affixing methods suited to different environmental conditions.
Asset tags can take various forms (such as RFID tags, barcodes, or QR codes) with each form suited to different tracking needs. It allows organizations to track the movement, usage, and maintenance of their assets, ensuring that nothing falls through the cracks.
For example, a QR code on a piece of equipment can link directly to its maintenance history, warranty information, and current status, streamlining both routine checks and emergency repairs.
This process is equally valuable for tracking intangible assets, helping companies safeguard intellectual property and ensure compliance with licensing agreements.
In today’s fast-paced business environment, the ability to track and manage assets (whether fixed or intangible) is one of the most important factors in reducing loss, optimizing resource allocation, and maintaining compliance.
📌 Asset tagging transforms static inventories into dynamic, actionable data, empowering companies to make informed decisions and respond quickly to operational needs.
What are the benefits of asset tagging?
Asset tagging delivers a host of tangible benefits for businesses striving to manage their resources efficiently and stay ahead in today’s competitive landscape.
By applying asset tags to physical assets such as equipment, vehicles, and office furniture, companies gain unparalleled visibility into the location, status, and condition of their assets.
This real time tracking capability streamlines asset management, making it easier to schedule maintenance, reduce downtime, and extend the useful life of valuable equipment.
The use of asset tags also enhances operational efficiency by simplifying inventory processes and reducing the risk of loss or theft.
With accurate tagging and tracking, businesses can quickly identify missing assets, allocate resources more effectively, and avoid unnecessary purchases or replacements.
This level of control supports better decision-making around investments, budgeting, and resource allocation, minimizing unnecessary expenses, and ensuring that every asset is used to its fullest potential.
From an accounting perspective, asset tagging provides the data needed for precise financial reporting and compliance.
Companies can track depreciation, monitor asset utilization, and ensure that all assets are properly accounted for in their books.
The benefits extend to improved maintenance planning, as real time tracking allows for proactive scheduling of repairs and servicing, minimizing unexpected breakdowns and associated costs.
Ultimately, asset tagging is a cornerstone of modern asset management, empowering businesses to optimize their operations, protect their investments, and maximize their return on every asset.
Whether tracking office furniture, vehicles, or specialized equipment, the right tagging strategy delivers efficiency, security, and peace of mind.
HVAC/R Assets: The Core of Your Operations
In the HVAC/R industry, assets aren’t just line items on a balance sheet; they are the very heartbeat of comfort cooling and refrigeration.
These critical fixed assets, such as chillers, unitary systems, commercial refrigeration racks, cold storage evaporators, and even specialized equipment like ice machines and refrigerated transport units, represent significant investments and are central to daily operations.
Unlike abstract financial assets or intangible intellectual property, these are tangible, physical units that require ongoing, meticulous maintenance and careful management to preserve their value and minimize costly downtime.
Regardless of their specific function – whether maintaining precise temperatures in a data center, preserving food in a supermarket, or ensuring comfort in a commercial building – all HVAC/R assets must be tracked and managed effectively.
Asset labels and tags are indispensable tools for monitoring the location, condition, and usage of these crucial pieces of equipment.
By implementing a comprehensive tagging system, businesses can ensure that every HVAC/R asset is accounted for, properly maintained, and leveraged for maximum benefit, directly impacting operational efficiency and profitability.
🏷️ Robust asset management is the absolute foundation of regulatory compliance and operational excellence in HVAC/R.
By deploying a comprehensive asset management system, businesses can maintain detailed records of their HVAC/R assets, including critical refrigerant data, precise maintenance schedules, and real-time tracking information.
HVAC/R Asset Management: Laying the Groundwork for Compliance
This level of oversight is essential not only for accurate financial accounting and tax reporting but, more critically, for meeting the stringent, ever-evolving EPA compliance requirements for comfort cooling and refrigeration.
Tamper-evident asset labels and durable asset tags play a crucial role in safeguarding these assets against unauthorized removal or tampering, providing an added layer of security and accountability.
With advanced technology and integrated systems like Tag Wizard, companies can monitor their HVAC/R assets in real time, quickly identifying any discrepancies or potential security breaches related to refrigerant containment.
This proactive approach not only protects valuable equipment and refrigerant charges but also ensures that businesses can respond swiftly to any compliance issues, avoiding costly penalties.
Effective HVAC/R asset management processes involve regular audits, immediate updates to refrigerant and equipment data, and continuous improvement of tracking systems.
By keeping asset records current and leveraging the latest technology, companies can dramatically reduce the risk of non-compliance, avoid devastating fines, and maintain a strong reputation within the industry.
Ultimately, laying the groundwork for compliance through diligent asset management enables HVAC/R businesses to operate with confidence, knowing that their comfort cooling and refrigeration assets are secure, their data is accurate, and their operations are fully aligned with regulatory standards.

The Ignored Warnings. John Peterson’s Nightmare.
John Peterson is the seasoned operations manager, the dedicated professional who’s always strived to do things by the book. He knows the right thing to do, but lately, “the right thing” has gotten exponentially harder.
His story is the industry’s story – a relatable journey through the escalating complexity of regulatory compliance, representing countless businesses and individuals who are simply trying to navigate a fundamentally changed landscape. His nightmare is a mirror for every business facing these new realities.
The first email landed in John’s inbox back in late 2023. A dry, official-looking missive about “Technology Transition Final Rule” and “compliance dates.” Like so many, he skimmed it, maybe flagged it for “later,” then buried it under the avalanche of daily operational fires. Business hummed along.
Then came the letter. Not to John directly, but to the corporate legal department. More formal, more pointed, referencing specific CFR sections and upcoming January 2025 compliance dates. Legal sent a terse summary, advising “awareness.” John’s eyes glazed over. More bureaucracy. More paperwork. It felt distant, abstract.
Until one Tuesday morning. No knock at the service company’s main entrance. Instead, a sleek black sedan pulled up to the loading dock. Two figures, crisp in state environmental agency uniforms, bypassed the front office, showed their badges to a startled security guard, and stated, “We just need access to the machine room. Unscheduled inspection, per the Technology Transition mandate.” John was about to find out that only his newest equipment had the right labels, and even that was not accurate.
The reality? John and all of us are all part of the 99% of businesses operating with equipment that is missing 99% of the right label data. Or, worse, labels that are already obsolete, illegible, or flat-out wrong. This isn’t theoretical; it’s a direct path to enforcement action. Non-compliance can mean losing significant money through fines, penalties, and the broader economic impact on your business’s financial assets and cash flow. Equipment with missing or incorrect labels is treated differently under the law, often resulting in immediate penalties or escalated enforcement.
🏷️ Your equipment’s label is no longer a suggestion; it’s its legal passport.
If that passport is faded, incorrect, or missing critical stamps, your asset is considered non-compliant.
The EPA isn’t sending a warning letter; they’re sending an enforcement team.
Compliance is now strictly controlled by regulatory agencies, ensuring that only properly labeled equipment remains in operation.
And their partner? Often, the Department of Justice.
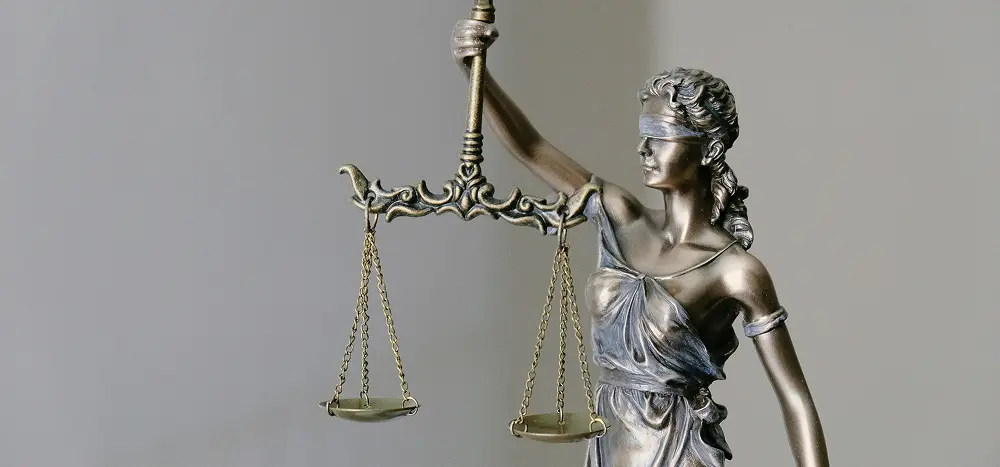
How We Got Here: The Unfolding Saga of HFC Regulation
Just imagine, the agents moved through John’s machine room, their methodical pace a stark contrast to his rising panic, he felt a cold clarity. This wasn’t arbitrary.
This was the culmination of decades of policy, born from environmental necessity and now enforced with surgical precision.
Asset tracking technology, such as RFID, has its origins in the Second World War and has since evolved to support modern compliance and asset management needs.
The AIM Act (American Innovation and Manufacturing Act) of 2020
This was the legislative earthquake. Congress empowered the EPA to tackle HFCs head-on, establishing three critical pillars:
Phasedown
A steep, aggressive reduction in the production and consumption of HFCs. Less virgin gas hitting the market each year
Technology Transition
This is what was hitting John now. It’s about restricting the use of high-GWP HFCs in new equipment across specific sectors. This pillar is the foundation for the granular labeling rules, forcing the industry to pivot to lower-GWP alternatives.
Refrigerant Management
Rules for handling, reclaiming, and disposing of HFCs to minimize leaks and maximize reuse. This includes the new 15 LB+ rule and stricter record-keeping.
The Technology Transition Final Rule (October/December 2023):
This wasn’t a proposal that vanished into the ether.
This final rule translated the AIM Act’s “technology transition” pillar into concrete, legally binding compliance dates and technical requirements. It’s the culmination of years of data, public comments, and industry feedback, refined into a granular set of rules for various subsectors.
The processes involved in implementing these new standards require careful coordination across compliance, reordering, and maintenance activities.
The EPA isn’t doing this to be punitive.
They’re doing it because a sustained supply of reclaimed HFCs is absolutely essential to service the enormous installed base of HFC equipment as virgin HFC production steeply declines.
Without tight controls and crystal-clear visibility into what refrigerants are where, the market faces catastrophic shortages post-2028.
Proper, accurate, and durable labeling is the bedrock for that visibility and control, ensuring reclaimers know what they’re getting and the supply chain isn’t rife with “phantom” gas.
The economic impact of these regulations is significant, as companies must allocate resources to ensure compliance and maintain operational continuity.

The Unforgiving Mandate: What’s REQUIRED on Your Equipment Labels
The agent stopped at a new residential split system, installed just last month. “Mr. Peterson,” she stated, her voice devoid of emotion, “this unit falls under the Stationary Residential and Light Commercial Air Conditioning and Heat Pumps subsector.
Its compliance date for manufacture and import was January 1, 2025. Let’s examine the label.”
The EPA has specified clear “Labeling Profiles” (ranging from Profile 1 to Profile 4) under 40 CFR 84.58.
These aren’t suggestions; they are the granular requirements that dictate exactly what information must be present on your equipment. While the exact combination varies by subsector, the core requirements are unforgivingly precise:
When considering the types of equipment and assets requiring labels, it is important to note that both current assets (such as cash, cash equivalents, and inventory) and fixed assets (like HVAC units, machinery, and other equipment) are included.
A fixed asset is a long-term resource such as a plant, building, or equipment, and vehicles like cars and trucks are typically depreciated over five years according to IRS guidelines.
Universal Core Labeling Elements (Required across all Profiles)
ASHRAE – Chemical Name
“R-410A,” “R-32,” “R-134a.” Not “Coolant” or a generic brand name. The label must use the ASHRAE refrigerant designation or the full chemical name for unregulated substances.
Why this matters
Clarity. This standardizes identification across the industry, leaving no room for ambiguity that could lead to mixing incompatible refrigerants or misidentifying materials for reclaim.
Full Date of Manufacture (or Model Year/Commissioning Date)
The exact month and year the equipment was manufactured or imported. For certain transport refrigeration or custom-built systems, it might be the model year or commissioning date.
Why this matters
This is the EPA’s timestamp. It allows them (and you) to instantly determine if the equipment was placed on the market after its sector’s compliance date, and thus, if it should meet the new GWP limits.
It’s your unit’s birth certificate for compliance. Accurate labeling is also essential for financial accounting and tax compliance, as it supports proper asset tracking and reporting.
Capacity Weight Listed
The precise refrigerant charge size in pounds or kilograms. No rounding.
Why this matters
This verifies compliance with GWP limits tied to charge size (e.g., “less than 200 lb” vs. “200 or more lb” in Industrial Process Refrigeration). It also provides crucial data for leak rate calculations, allowing technicians to immediately know how much refrigerant should be in the system, and aids in accurate record-keeping.
“For Servicing Existing Equipment Only” (If Applicable)
If a component or system is intended only for servicing older equipment that uses high-GWP refrigerants above the new limits, it must be clearly labeled with this specific disclaimer.
Why this matters
This prevents high-GWP components from being accidentally or intentionally installed in new systems, undermining the phase-down. It’s a critical guardrail against backsliding.
Durable – Weather Proof
The label must be able to withstand the environmental conditions the equipment will endure throughout its operational life.
This means resisting UV, moisture, extreme temperatures, and chemicals.
Metal asset tags, such as those made from aluminum or other metal alloys, are often used for their durability and ability to withstand harsh environments.
The most common types of asset tags include foil, anodized aluminum, polyester, and vinyl, chosen for their resistance to abrasion and chemicals.
The expected lifespan of asset tags is a key consideration, and several methods (such as pressure-sensitive adhesives or mechanical attachments) are used to ensure longevity and secure application.
Why this matters
A faded, peeling, or unreadable label is a useless label in the eyes of the EPA. And a useless label is a non-compliant label, triggering presumptive violations.
Readily Visible
The label must be easily found and read without requiring disassembly, special tools, or contorting into impossible positions.
Proper label visibility and legibility are crucial for protecting the monetary value of assets and ensuring that their identification supports ongoing asset management.
Why this matters
If an inspector can’t easily see it and read it without effort, it’s presumed non-existent.
Contrasting Color
The text must stand out clearly against the label background to ensure maximum legibility.
Why this matters
Clarity is paramount; no squinting or guessing allowed.
When considering the types of equipment and assets requiring labels, it is important to note that both current assets (such as cash, cash equivalents, and inventory) and fixed assets (like HVAC units, machinery, and other equipment) are included.
📌 Asset tags are used to track and manage these assets, supporting accurate accounting and compliance.
While HCFC recovery from fire extinguishers does happen, reclamation processes are hindered by restrictions due to the proprietary compositions of the agents and complex blends.
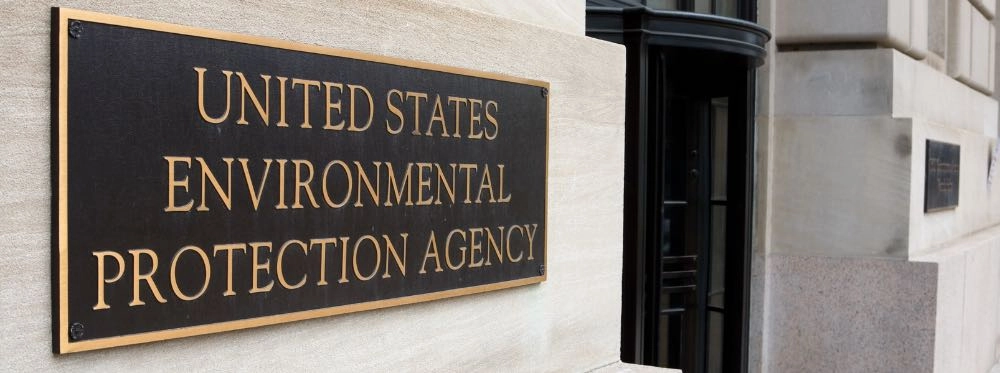
The Devil is in the Detail: Subsector-Specific Details
Self-Contained Units (Residential AC/Heat Pumps, Household Refrigerators, Vending, Retail Standalone, Motor Vehicle AC, Dehumidifiers)
These, hitting January 1, 2025 compliance dates, largely fall under Profile 1.
They demand the core elements and adhere to strict GWP limits (e.g., 700 for AC/dehumidifiers, 150 for household/vending).
Industrial Process Refrigeration (Various Dates: Jan 1, 2026, 2028)
These often use Profile 1 or 3, introducing complexities like specific notes about charge size (less than 200lb, 200lb or more) or high/low temperature side of cascade systems, with GWP limits spanning 150 to 700. Some applications might be “Not Covered.”
Label implication
If your equipment has a charge of “200 or more lb” and a 150 GWP limit, the label needs to reflect both the GWP limit AND the charge size indication as per Profile 3.
Self-Contained Automatic Commercial Ice Machines (Jan 1, 2026/2027)
These can be Profile 1 or Profile 3.
Crucially, if it’s a batch type (above 1,000 lb harvest rate) or continuous type (above 1,200 lb harvest rate), specific prohibited substances are listed, and the label must declare the GWP limit or prohibited substance.
Profile 3 for remote ice machines specifically requires the harvest rate to be noted on the label.
Cold Storage Warehouses (Jan 1, 2026/2027)
These are typically Profile 1 or 3, with GWP limits of 150 or 300, and often requiring indication of charge size (e.g., “charge size over 200 Lbs” for Profile 3).
Refrigerated Transport (Jan 1, 2025)
Including intermodal containers and road/marine self-contained products. These fall under Profile 2 or 4, with a 700 GWP limit for intermodal or specific prohibited refrigerants for road/marine.
Label implication
Profile 2, for example, specifies “Model Year” for the date of manufacture, aligning with common vehicle industry norms.
Chillers (Various Dates: Jan 1, 2025, 2026, 2028)
Many industrial process refrigeration chillers fall under Profile 3, with GWP limits of 700. Comfort cooling chillers, a later compliance date, will also adhere to specific GWP limits.
Ice Rinks (Jan 1, 2025)
These require Profile 3, with a 700 GWP limit.
The financial implications of compliance include not only the expenses related to the purchase and application of asset tags, but also the monetary value assigned to each asset, which must be accurately recorded for accounting and reporting purposes.
Proper asset tagging supports the recognition of economic benefit and potential income from asset utilization, while also ensuring that liabilities, loans, and securities are properly managed in the event of non-compliance.
Documenting the purchase of assets and the use of asset tags is essential for maintaining accurate records of purchased assets and supporting financial accounting standards.
📌 These exemptions are strictly for testing purposes, essential for demonstrating functionality, and do not cover the emergency use of HFCs for actual fire suppression.
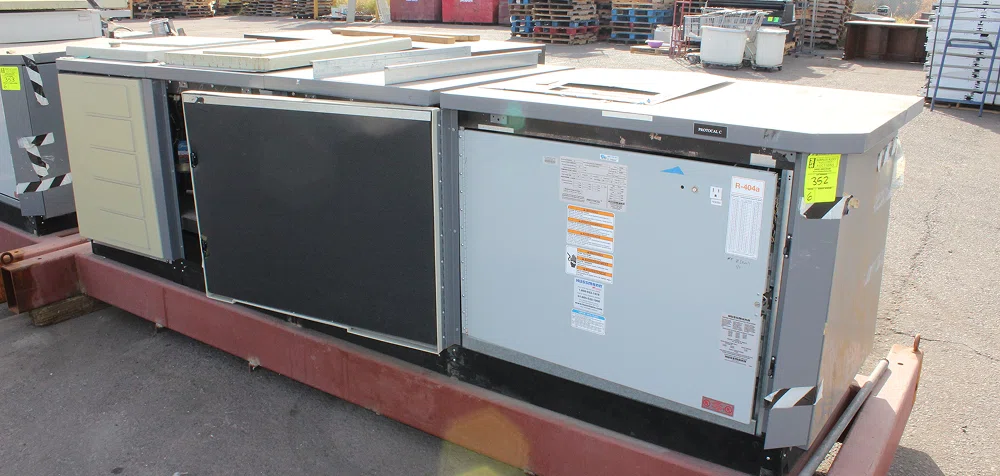
Faded, Bad Data, and Missing Labels
John’s face paled as the agent moved to an older, but still operational, supermarket refrigeration system.
The original label was barely visible, a sun-baked ghost of its former self. “Mr. Peterson,” the agent stated, “this label is illegible.
Therefore, under 40 CFR 84.58(e), this unit is presumed to contain a prohibited HFC, installed after the compliance date for this subsector. We’ll be documenting this as a violation.”
This scenario plays out daily because, based on field observations and common industry practices, the vast majority of existing labels on HFC equipment are a compliance disaster:
Faded into Oblivion
How many outdoor units, rooftop chillers, or transport refrigeration units have labels baked by the sun, washed by rain, or blasted by chemicals until they’re ghost images?
If an EPA inspector can’t read it, it’s a missing label.
This isn’t theoretical; it’s happening right now in your facilities.
Proper labeling is essential for maintaining control over tangible assets, ensuring that each physical unit is properly identified and managed as a controlled resource.
The “Bad Data” Catastrophe
Outdated Info
Your equipment might have met standards when built. But what if regulatory changes (like new GWP limits for certain applications) have made that data obsolete? Or what if a system was retrofit with a different refrigerant and the label wasn’t immediately and accurately updated? An outdated label is a false statement to the EPA. The benefit of maintaining accurate and controlled asset records is that it helps avoid costly compliance violations and supports better decision-making.
Retrofit Roulette
If a system has been retrofitted with a different refrigerant (especially a lower GWP one) and the original label wasn’t meticulously covered or updated with the new, correct, compliant information, you’re presenting false data. An incorrect label is just as bad as a missing one, implying deliberate deception.
Incomplete Data
Missing serial numbers, vague refrigerant descriptions, approximated charge sizes. These might have flown under the radar before, but with the new detailed profiles, they’re red flags.
The “Missing” Problem (and the “Presumed Guilty” Rule)
Many companies simply lack the robust, centralized systems to ensure every single unit manufactured, imported, or installed after January 1, 2025, has the correct, durable, and visible label.
And if that label isn’t there, or is illegible, the EPA’s stance is clear: your equipment is presumed to contain prohibited, high-GWP substances.
That’s not an accusation; it’s a legal finding until you can prove otherwise.
Keeping asset data current and compliant requires ongoing processes such as regular label inspections, updates, and documentation.
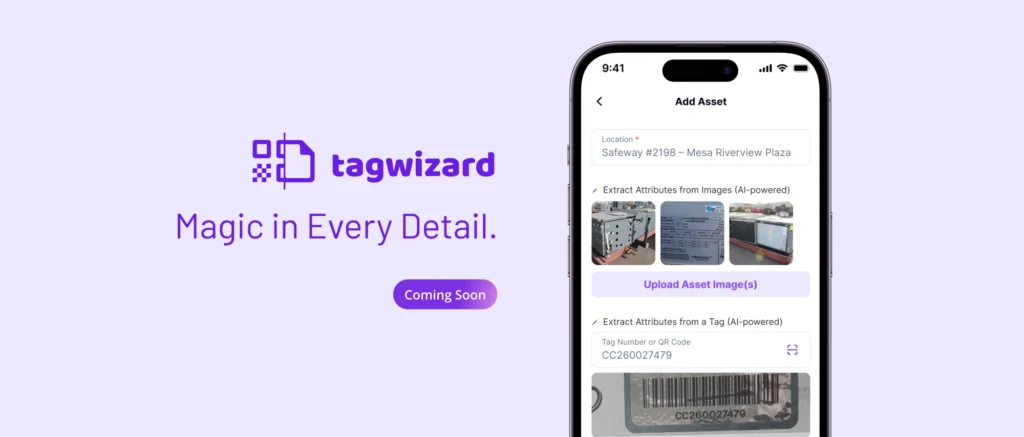
Best Practices for Mastering Asset Tagging with Tag Wizard
Implementing a successful, compliant asset tagging program in this new regulatory landscape demands more than just sticking labels on equipment.
It requires a strategic approach, powered by the right tools.
To truly unlock the benefits of meticulous asset management and navigate the EPA’s unforgiving demands, companies must embrace these best practices, and our asset tagging app Tag Wizard is built to make every single one achievable for your entire team.
Choose the Right Label Material & Ensure Durability
The Challenge
Your labels are your legal proof. They must withstand brutal environments, from rooftop sun to chemical exposure, remaining perfectly legible for years. Faded labels are non-compliant labels.
Tag Wizard’s Solution
While Tag Wizard doesn’t manufacture labels, it empowers you to source EPA-compliant, durable label materials directly from the app, anywhere you are.
It ensures you’re using materials designed to meet the “permanent, durable, readily visible, and legible” requirements, giving you confidence that your tags won’t fail when an inspector arrives.
Standardize the Asset Tagging Process (Effortlessly):
The Challenge
Consistency is paramount. Without clear, easy-to-follow guidelines for how assets are tagged, what information is included, and where labels are placed, your data becomes a chaotic mess.
Tag Wizard’s Solution
Our asset tagging application, Tag Wizard, digitizes and standardizes your entire tagging workflow.
Every team member, armed with just a smartphone, follows the same intuitive prompts within the app.
This ensures consistent data capture, correct label placement, and uniform information across your entire refrigerant asset base, making training simple and compliance automatic.
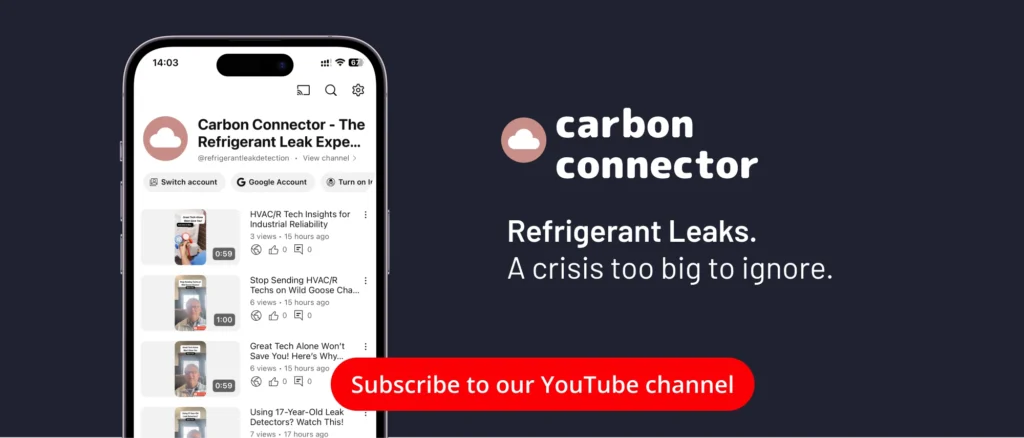
Keep Asset Data Up to Date (In Real-Time):
The Challenge
Asset management is only as good as its data. Manual updates are slow, prone to error, and quickly outdated, leading to dangerous discrepancies during audits.
Tag Wizard’s Solution
Our asset tagging app transforms data maintenance into a real-time, collaborative effort.
Every team member can instantly update HVAC/R asset records to reflect changes in location, status, ownership, or refrigerant type directly from their mobile device.
This ongoing, immediate maintenance helps prevent discrepancies and ensures your tracking remains flawlessly accurate.
Integrate with Comprehensive Asset Management Systems
The Challenge
Isolated tagging efforts provide limited value. True control comes from connecting your tagging process to a robust, centralized system.
Tag Wizard’s Solution
Our HVAC/R asset tagging app is designed for seamless integration.
It acts as the intelligent mobile front-end to your comprehensive asset management system, enabling real-time tracking, automated alerts for maintenance needs, and comprehensive reporting.
This integration gives you unparalleled control over your HVAC/R assets, streamlines operations, and significantly reduces maintenance costs.
📌 Clear guidance is essential for industry-wide compliance and sustainability.
Connect with us to stay ahead of evolving RCRA regulations and ensure your team is prepared.
Conduct Regular Audits and Inspections (With AI Assistance)
The Challenge
Periodic reviews are essential to catch missing or damaged labels, outdated information, and process gaps. But manual audits are time-consuming and prone to human error.
Tag Wizard’s Solution
Tag Wizard revolutionizes audits. Your team can conduct inspections directly from their smartphones, quickly verifying labels.
For those frustrating, faded tags, Tag Wizard’s AI-powered tag reading steps in, helping to decipher critical information that would otherwise be lost. This makes audits faster, more accurate, and ensures continuous compliance.
By integrating our app Tag Wizard into your operations, you’re not just following best practices; you’re leveraging cutting-edge technology to achieve greater efficiency, lower compliance risks, and enhanced control over your physical assets.
Tag Wizard doesn’t just protect your investments; it provides the data-driven insights needed to drive business success in this demanding new era of refrigerant management.
📼 Subscribe to Our YouTube Channel
Real HVAC/R and compliance challenges—turned into clear, actionable insights. Watch expert webinars, get practical tips, and learn from real-world case studies.
The Dividends: The Cold, Hard Truth of This New Reality
John’s mind reeled. He’d always believed the EPA’s focus was solely on preventing leaks. But a colder, more pragmatic truth hit him: This new era of stewardship isn’t just about emissions; it’s a relentless pursuit of due diligence, exposing every administrative gap and revealing the economic benefit of diligent compliance .
This is not business as usual. The EPA knows much of this refrigerant leaks. Their paramount concern is the loss of potential replacement refrigerant. As virgin HFC production plummets, the industry will depend entirely on reclaimed supply.
These regulations aren’t just about environmental idealism; they’re about maximizing capture, tracking, and reuse of every pound of HFC in circulation.
The “dividends” of this new reality are a direct result of an iron-fisted focus on administrative control, data integrity, and supply chain resilience.
Compliance doesn’t just protect you from fines; it safeguards the very refrigerant you’ll need to stay in business. Retained refrigerant represents a significant economic benefit and holds substantial monetary value, as it can be reused or sold, directly impacting your bottom line.
This is about survival, driven by the cold logic of supply and demand.
Effective compliance also means managing your resources efficiently, which can provide businesses with the potential for additional income and benefit through reduced losses and improved asset utilization.
⏳ Forget “Upcoming” Deadlines.
The cold, hard truth is this: the milestones are already in motion, and the race is already being run.
The Race is On: Milestones Already in Motion, Compliance is Non-Negotiable
The path to full compliance with the EPA’s Technology Transition and refrigerant management rules isn’t a future planning exercise; it’s a current, accelerating reality. The agency has adopted a phased approach, yes, but that “phase” started years ago, and the critical checkpoints are hitting now.
For instance, by January 1, 2028, it won’t be a suggestion: certain types of equipment will be required to use reclaimed HFCs for their initial charge.
This isn’t a distant goal; it’s a monumental shift in sourcing and supply chain management that demands immediate preparation.
Similarly, new equipment installations aren’t getting a grace period; automatic leak detection systems must be operational within 30 days of installation, ensuring immediate, real-time compliance with monitoring requirements.
This isn’t about submitting comments on a proposed timeline anymore. It’s about acting now to ensure your operations are not just “aware” but compliant.
This means a ruthless review of your current equipment, a complete overhaul of installation and servicing procedures, and ensuring that all documentation and reporting are not just accurate, but meticulously aligned with the latest EPA regulations.
The time for passive engagement is over. The race for compliance is already underway, and every missed milestone is a step closer to a violation.
Staying ahead of the curve isn’t an option; it’s the only way to ensure your operations remain viable and ready for the unavoidable future of refrigerant management.