
How Trakref + Fexa Are Transforming the Work Environment and Compliance Culture in HVAC/R
The Milestone That Changes Everything
Every industry has a moment where what’s been considered niche becomes the norm. With the launch of the integrated API over at Trakref/Fexa, that moment is now.
Compliance is no longer an afterthought.
It’s mainstream, and the native integration between Trakref and Fexa marks the official shift. When we sold Trakref nearly 2 years ago, this was the goal, to bring compliance mainstream without competing with the importance of the CMMS systems but instead working together to address the challenges of operationalizing climate change and regulatory compliance.
This isn’t a patch or a workaround. It’s a milestone. With this milestone comes a new standard—real-time regulatory alignment inside your CMMS.
This integration will help organizations comply with new regulations, shifting from a reactive to a proactive approach, improving both environmental impact and operational efficiency by reducing greenhouse gas emissions, in real-time and lowering the labor burden needed to meet those goals.
Fexa’s “Blue Water” strategy is all about transforming the way facilities manage work, unlocking new value by removing legacy constraints.
Trakref has been on its own Blue Water journey, defining a third way for compliance software—structured, responsive, asset-centric, and operationally embedded.
Together, these platforms deliver something the HVAC/R industry has never had: an intelligent, guided, and rules-based work environment that is both regulatory-compliant and technician-friendly.
What Was CMMS in Facilities Management (And Why This Change Matters)
Let’s be honest—CMMS used to mean something very different. It stood for spreadsheets with a dashboard, invoice wrangling, and work order chaos.
Sure, it was a better version of binders and sticky notes, but it wasn’t built for regulatory depth. It was a cost-control tool, not a compliance engine.
For years, teams have tried to force compliance into CMMS systems. It never stuck. Why?
Because those platforms were too loose. They’d bend their logic to match the customer’s preference—even if it meant breaking with what the regulations actually required.
Client services play a crucial role in collaboration among various teams, including operations and sustainability, to develop a unified approach to managing refrigerant emissions. By integrating advanced technology, we can better manage refrigerant emissions and contribute to the fight against climate change.
I was on the front line of this development for more than 10 years, originally before Trakref existed we tried everything to get CMMS companies to embed the logic of regulatory requirements into their work product – and to no avail, so with a small group of people we created an innovation research lab, back at Polar Technology in 2008 ( the original reclaim company I had founded in 1993) and that’s where Trakref incubated and developed concepts like tagging and labeling, asset-centric compliance, distributed regulatory logic.
By the time we founded Trakref into a business, we had introduced the concept of refrigerant management to many CMMS companies some tried to copy the idea – but they did it as a CMMS company would do it, and others just ignored it and assumed their clients were responsible for the challenge of integration and this was where the Swivel Chair was born.
The Third Way
Back in 2011, there were two models for managing HVAC/R compliance data.
When we started building what would become Trakref, it wasn’t because we wanted to build software—it was because we had no other choice.
We were in the middle of a problem the entire HVAC/R industry was pretending didn’t exist. Compliance wasn’t just a paperwork issue—it was broken at the workflow level. And the software that existed at the time? It just made things worse.
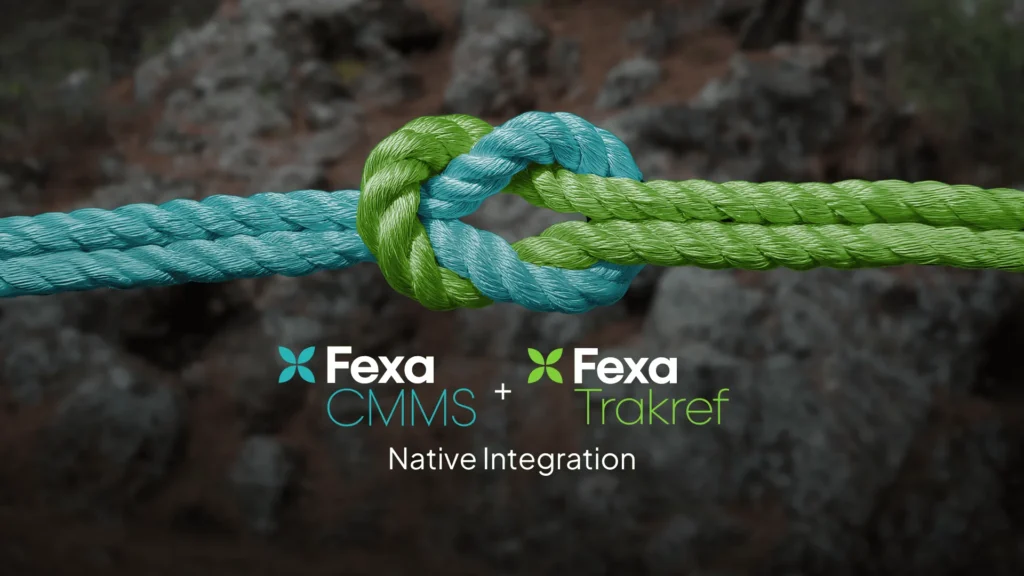
Everything we saw fell into one of two categories, which makes sense given the historical focus on immediate needs rather than long-term sustainability.
Addressing climate change requires a shift from short-term fixes to sustainable, long-term solutions.
1. Centralized Admin Systems
These were the “enterprise” tools. Large, powerful, and painfully manual.
They relied on a single person—usually an overworked admin or office manager—to collect, interpret, and enter service records from dozens or even hundreds of techs. That person had to sort through paper tickets, decode handwriting, and figure out what was worth entering and what was guesswork.
If that admin takes a vacation, goes out sick, or just gets overwhelmed?
- The system backs up instantly.
- Paperwork piled up.
- Inspections got missed.
- Compliance stalled out.
I remember one job where I was called in to help a major facility prep for an audit. Their admin had been out for two weeks. The stack of unentered tickets was literally held together with rubber bands.
It was a mess—and every ticket represented a leak, a service call, or a refrigerant charge that had zero digital traceability. The techs were doing the work, but the system couldn’t see it.
That wasn’t a software solution. It was a bottleneck with a login screen.
2. Early SaaS Tools
Then came the SaaS wave—sleek interfaces, web-based access, and mobile-first features.
But these solutions had a fatal flaw: they didn’t guide anyone.
Instead of enforcing rules, they handed that job to the field team. Every tech had to remember what the EPA required. What the inspection intervals were. Whether the charge size hit a reporting threshold.
Whether the asset class changed how refrigerant usage had to be logged.
This was nearly impossible since the regulations are always changing, and there are more than 40,000 pages of published regulations related to HVAC/R and refrigerants.
They were expected to know everything, and the software just waited for them to fill in the blanks.
The result? Bad data. Missing steps. Inconsistent records. And no accountability—because the system wasn’t built to enforce any.
Every company that seemed to fail an EPA audit had a software tool in place, and they still managed to fail. (At Trakref, we never let anyone fail, and that legacy continues to this day)
I remember one grocery chain that had recently deployed one of these SaaS tools. Their techs were sharp. They were diligent. But the system treated every asset the same, every work order like a blank canvas.
Compliance wasn’t built in—it was bolted on. Within six months, they had hundreds of work orders with incomplete refrigerant data. And they didn’t even know they had a problem until I showed them.
Another time, I remember walking into a grocery, nice operation, great people, and behind the desk of one team member was a stack of work orders that was 3 feet high by 3 feet wide, numbering more than 4000 work orders, all still unrecorded in their refrigerant management software system. Because one person was responsible for reviewing and entering all the records, then approving, denying, and entering the responses – that’s the only way they could make sure the data was accurate.
So We Built the Third Model
That’s when it clicked for us.
If we were going to make a real difference, we couldn’t just track compliance —we had to provide a decentralized way to gather data and enforce requirements.
Not in a heavy-handed way, but in a smart, responsive, guided way that made sense to the people doing the work.
We had to build a system that:
- Understood regulations at the asset level
- Prompted the right questions at the right time
- Structured workflows around real-world service conditions
- And protected compliance by design, not after the fact
That became the foundation of Trakref. We didn’t copy what others were doing—we rejected it. We knew that techs shouldn’t have to be legal experts. Admins shouldn’t carry the whole burden. And compliance shouldn’t live in a separate tool.
We built something different because the industry needed something different.
And now, with Fexa fully integrated into that model, they’ve made that goal a reality.
They are no longer just tracking work – they are guiding it.
They are not just storing data – they are applying rules that matter.
And they can do it in real-time, for real people, in real-world jobs that can’t afford to get it wrong.
Experience and listening paved the way

2008 – It all started when I was asked to audit a paper trail for a company under investigation by the EPA. The company trusted our reporting results from Polar.
We had a fully transparent material movement history in our compliance tool because we were using an innovative emerging tech, called Block Chain (back in 2008 no one had ever heard of this) to track refrigerant at every phase of development with a highly structured and easy to use 14 step part numbering system, that was deployed through an online banking application we built to track cylinders and refrigerant gasses.
Responding to the industry’s need for enhanced refrigerant tracking, we developed a smart system, as detailed in patent application US 20170116654 A1, designed to streamline management and improve compliance.
Imagine a digital tracking system for the refrigerant industry, a detailed, real-time inventory and status report accessible via web and mobile apps. This system was created through a collaborative effort, with a strong emphasis on direct feedback from industry professionals facing the challenges of effectively tracking refrigerants.
The core goal was to provide a practical solution, and the resulting system offers:
Real-time, End-to-End Visibility
Addressing the crucial need for comprehensive tracking throughout the refrigerant lifecycle, from storage to recovery.
Simplified, Data-Driven Compliance
Automating data collection and reporting to ease the burden of regulatory requirements and provide actionable insights.
User-Centric Design and Accessible Data
Offering intuitive web and mobile interfaces that allow users to access critical information when and where they need it.
This project aimed to directly address the complex challenges of refrigerant management, helping businesses comply with regulations, ensure refrigerant quality, and gain valuable insights into the entire lifecycle. We’re encouraged by its positive impact on streamlining operations and improving sustainability practices within the industry.

Fexa got it from the beginning.
At Trakref, we knew we had a system with real logic, real rules, and a real purpose. For over a decade, we stayed in our lane—building a platform that honored the structure of refrigerant regulations, ESG reporting, and asset governance. We didn’t try to please everyone. We built it to work right.
But time and again, we tried to integrate with CMMS companies—you name one, and we tried to work with them—but each effort was a failure, and this was terrible for the end user because it meant the burden to manage this was 100% on them. We realized we had just met the right partner, so we kept at it.
Our goal was always to directly address compliance risks posed by increasing regulatory requirements from bodies like the EPA and SEC. By integrating compliance management into facilities and operations, we help navigate mounting cost pressures and sustainability goals, enhancing overall efficiency.
So when it came time to expand, we didn’t compromise.
We didn’t water it down. We looked for a partner who respected what we had built and had the muscle to take it further. Meeting after meeting failed, but when we got together with Marc at Fexa and the money people, they really saw the possibility, and right from the beginning, they were looking at this as a way to solve problems for their existing customers.
That partner was Fexa.
Thanks to one of my Board members, Dave Dutch, who knew a guy that knew a guy that worked for a private equity firm that owned an emerging Work Order management software company (CMMS) called Fexa.
Due to Dave’s help and amazing communication skills, the PE firm MainSail, and specifically the core team of Vinay and KC, opened their minds to the possibility and the needs that were being underserved, and they were willing to make an investment in the possibility, and that possibility is today.
Kurt & Steven seemed to dial in the right amount of investment and resources to make it happen, and they seem to really care and have an interest in seeing it through to the end.
When our UX guru, Julie, joined Trakref seven years ago, she began by conducting valuable user interviews and engaging in conversations that informed the development of the intuitive user experience we have today. Her contributions reflect a thoughtful collaboration with our users, gathering diverse insights that have been pivotal in driving meaningful solutions.
Although I am no longer an insider, we get together every month and we share stories about markets, history, relevance, and applicability.
They still have a long list of things to accomplish since the products are now much more versatile, but they now have a set of new tools that enable a broader future.
Unlike the others, Fexa didn’t ask us to soften the rules. They didn’t try to override our engine with a one-size-fits-all interface. They leaned in.
They preserved our logic. They built the integration around compliance, not in spite of it. That’s what makes this integration different. That’s why it works.
Because for the first time, a CMMS didn’t just absorb compliance. It respected it.
Fexa + Trakref: A Game-Changer for HVAC/R Compliance
The Next Level of Compliance Management, simplified by Fexa
Goodbye, Swivel Chair. Hello, Seamless Workflow.

Everyone has different priorities and perspectives
This evolved, and it is the byproduct of so many unique solutions, all solving a specific problem but lacking the integration needed to make life easier for people using them.
For a decade, facilities teams had to bounce between work order systems and compliance platforms. The data didn’t sync. The rules weren’t enforced. The result? Gaps, missed reports, costly fines, and overburdened technicians.
💡 Important Insight
Facility managers clearly benefit from this seamless integration—operations run smoother, and compliance becomes part of the workflow instead of a separate burden.
But here’s the problem: most CMMS platforms treat every asset like it is the same.
Add a few attributes here, toggle a few checkboxes there—maybe even customize the form layout.
And that word—customizable?
It’s the enemy of compliance.
We don’t get to customize the law.
We can tailor it to the context.
We can prioritize based on risk.
But compliance isn’t optional. It’s structured. It’s rule-bound.
So when software platforms leave it up to users to “configure it however they like,” they’re effectively saying:
“Compliance is your problem. Not ours.”
That’s not how we operate.
At Trakref—and now with Fexa—they enforce structure where it matters because that’s the only way to deliver real results.
It’s not an Integration; it’s a Convergence
Now:
- A technician opens a work order in Fexa.
- If refrigerant or compliance triggers are involved, the Trakref engine activates in the background.
- The workflow adapts based on refrigerant type, leak history, asset class, and regulatory jurisdiction.
- Real-time validation flags bad entries before they become violations.
- And data flows automatically between systems—no double entry.
This isn’t just integration. This is convergence. And it’s asset-centric, scalable, and ready for field teams.
Asset-Centric: the only way to work together
In HVAC/R, the asset is the source of truth. Every compliance obligation, inspection requirement, and reporting deadline ties back to the asset’s profile: its type, charge size, location, and service history.
Trakref pioneered an asset-centric compliance model:
- Each asset has a structured taxonomy and a unique digital nameplate.
- Changes to the asset’s profile (charge size, refrigerant, use case) automatically trigger updates to compliance requirements.
- Assets are organized with parent-child logic, enabling detailed reporting across complex facilities.
Assets aren’t just labeled.
They’re classified, governed, and linked through parent-child relationships so you can track systems, subcomponents, and service history with full clarity.
But here’s the truth: most CMMS platforms still don’t get this.

They treat HVAC assets—the ones driving 40% of your energy budget and more than 50% of your teams’ compliance risk—with the same governance logic as a parking lot light.
Same interface. Same data model. Just more fields…
- Their solution to complexity? They add fields.
- Want to track refrigerant? They add a text box.
- Need inspection dates? Here’s a dropdown.
❌ But they don’t autopopulate.
❌ They don’t enforce logic.
❌ They don’t adapt based on what type of system it is, where it is, or what regulations apply.
Because of that, you can’t benchmark anything.
You can’t measure across classes.
You can’t catch risk before it becomes a failure.
Everything becomes “loosy goosy”—a patchwork of preferences with no structure, no consistency, and no real value when it’s time to audit, report, or act.
✔️ That’s why structure matters.
✔️ That’s why we built Trakref around it.
✔️ And that’s why Fexa respected it instead of overriding it.
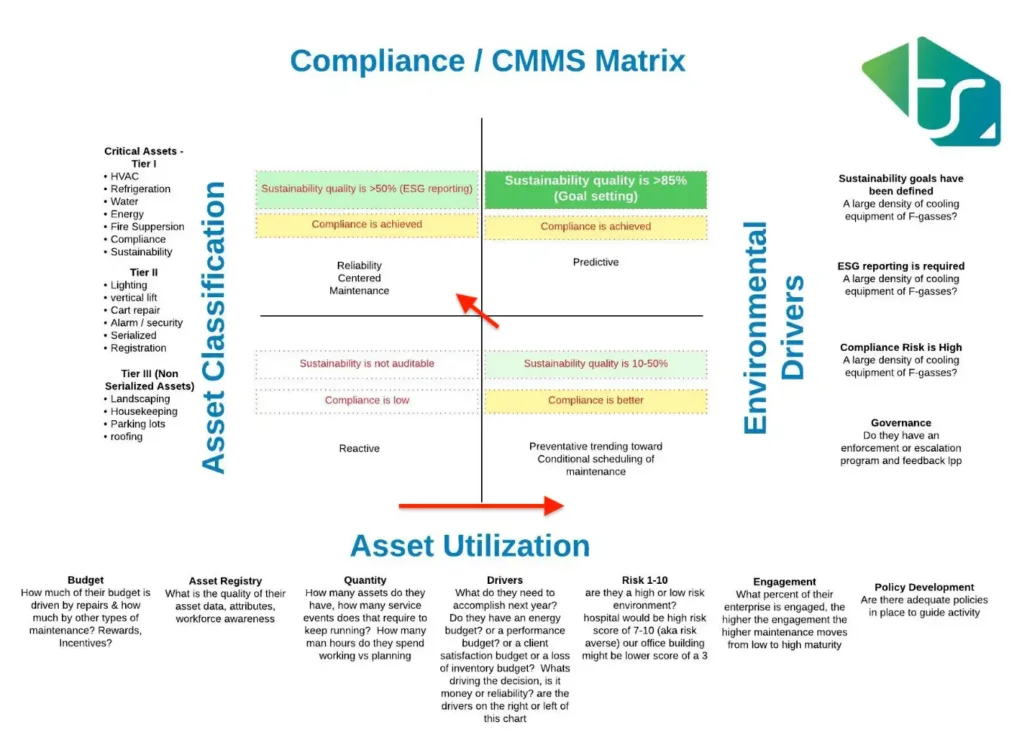
Governance: From Policy to Action
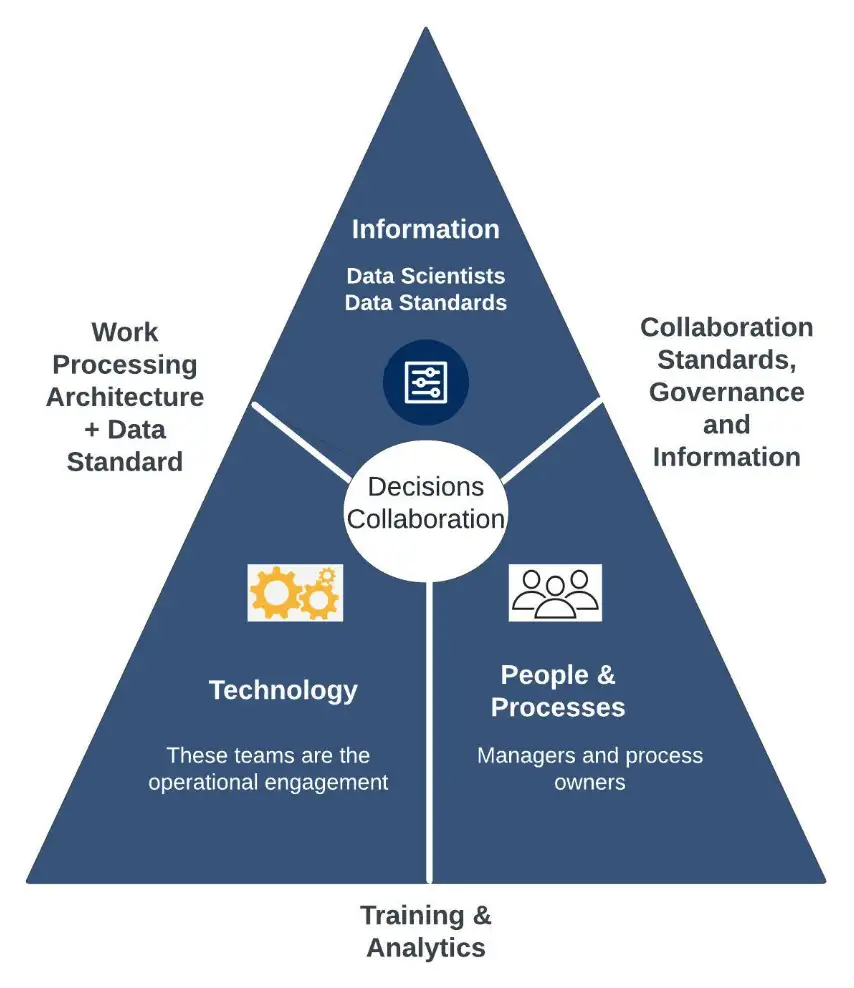
Governance isn’t paperwork. It’s action. It answers: Who can do what, when, and under what authority?
Fexa + Trakref bring governance into the workflow:
- Role-based permissions restrict who can edit, adjust, or deactivate assets.
- Compliance rules are enforced live—no need to audit after the fact.
- Every change has an audit trail, a timestamp, and a purpose.
By integrating innovative solutions, the governance workflow enhances compliance and efficiency, addressing sustainability goals and driving better outcomes for facilities and operations teams.
This is governance by design, not reaction. It supports multiple stakeholders:
- ESG teams need confidence in emissions data.
- Legal and compliance teams need transparency.
- Operations need speed without sacrificing control.
Now, compliance and governance are no longer at odds. They are one system, working in concert.
AIM Act Compliance and Regulatory Requirements
The AIM Act (American Innovation and Manufacturing Act) represents a significant regulatory shift, aiming to phase down the production and consumption of hydrofluorocarbons (HFCs) in the United States.
For facilities managers, compliance with the AIM Act is crucial to avoid penalties and protect their reputation. This regulation requires meticulous tracking and reporting of HFC emissions, as well as the implementation of measures to reduce these greenhouse gas emissions, which have a high global warming potential and significant environmental impact.
These measures are crucial in the fight against climate change, as HFCs have a high global warming potential.
Refrigerant management software plays a vital role in helping facilities managers track and report their HFC emissions accurately. It also identifies opportunities to reduce emissions, such as transitioning to low-GWP refrigerants and improving the energy efficiency of equipment.
Compliance with the AIM Act also involves ESG reporting, where facilities managers must document their progress in reducing HFC emissions.

Managing refrigerants in a sustainable and compliant manner is critical for facilities managers to achieve their sustainability goals and reduce their environmental impact. By leveraging advanced management software, facilities managers can ensure they meet regulatory requirements, contribute to environmental sustainability, and support their organization’s broader ESG objectives.
Compliance used to be the exception. Now, it’s embedded in every workflow. Thanks to Trakref’s rules engine and Fexa’s flexible platform, the integration can now deliver:
- Real-time refrigerant event tracking: leak inspections, repairs, top-offs, removals, and retrofits
- Audit-ready data with full traceability
- Mobile-ready field workflows
- Smart prompts and drop-downs that eliminate guesswork
- Role-based access that respects the chain of custody
This milestone doesn’t just improve compliance. It reshapes the technician’s experience. But remember, it is not just the AIM act; it’s everything, and it’s like building a house on quicksand.
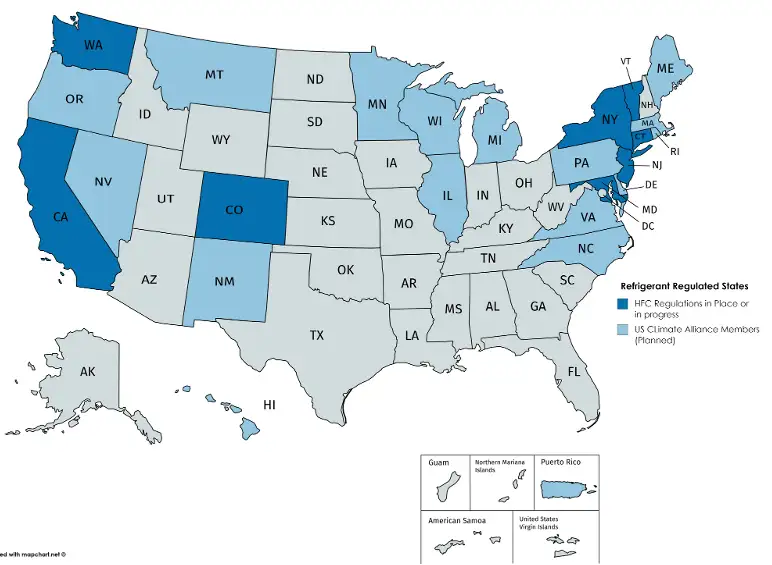
Compliance: From the Boardroom to the Boiler Room
As Chase Sanders often said, “Compliance runs from the boardroom to the boiler room.”
And he was right.
This isn’t just about ticking off EPA boxes.
It’s about trust, transparency, and accountability—everywhere.
- In the boardroom, compliance means meeting ESG targets, protecting brand reputation, and satisfying investors.
- On the ground, it means following the right steps, using the right materials, and staying ahead of audits, fines, and failures.
- In the software, it means rules are built in—not left to chance.
For years, compliance lived in silos:
- Legal teams built policy.
- Ops teams ran the buildings.
- And somewhere in between? A disconnect.
But not anymore.
With Trakref + Fexa, you can now design a strategy in the boardroom and see it executed in the boiler room with confidence.
The system doesn’t just collect data. It applies real-time logic, region-specific rules, and asset-level intelligence that syncs your policy with your practice.
Here’s what that looks like:
Need to report under CSRD?
💥 Bam—you’re covered. All the refrigerant logic is already mapped, and your audit trail is baked in.
Facing new California rules under SB 253 or CARB?
💥 Bam—got you covered. Inspection intervals, charge thresholds, GWP categories—it’s all live in the workflow.
Did the EPA just update the SNAP list or AIM Act reporting requirements?
💥 Bam—still covered. The rules engine updates automatically. No guessing. No re-training. No fines.
Only using Fexa and not Trakref?
You’re still covered. Thanks to Fexa’s smart wire-up into Trakref’s compliance layer, you can turn on rules-based workflows for any covered asset—without leaving your CMMS.
This is what it means to operationalize governance.
You don’t just hope your policy gets followed—you know it will.
Because the system checks, guides, and enforces it at every step.
And whether your building is in Berlin or Bakersfield, if compliance is on your scorecard, you’re covered.
🔑 Key Takeaway
Whether you’re in the U.S., Europe, Canada, or Washington State, the reality is the same: The burden is growing. The consequences are real.
What This Looks Like in the Real World
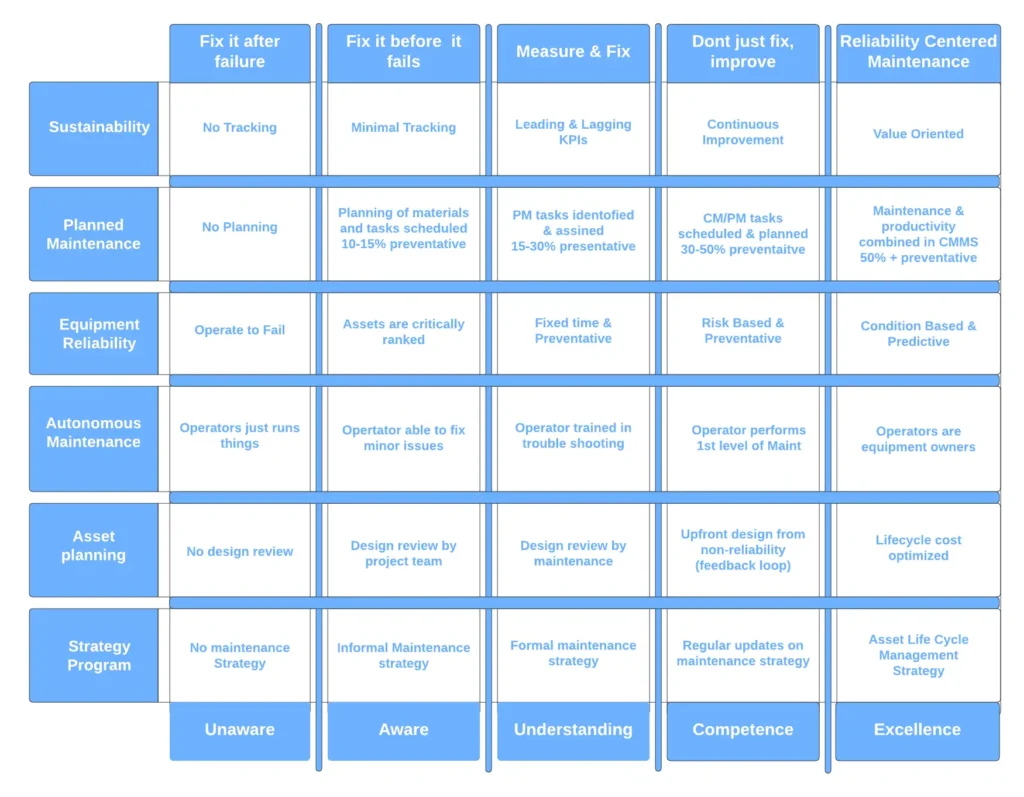
Let’s put this into perspective. Here are three quick snapshots of how this integration shows up in real-world workflows:
Scenario 1: The Grocery Technician
A tech receives a Fexa work order for a refrigeration rack that’s been underperforming. When they scan the asset, Trakref flags that it’s approaching a refrigerant threshold requiring a leak inspection. The work order dynamically updates with a compliance checklist. The technician follows prompts, logs refrigerant amounts, and closes out—no need to toggle between systems. The data is validated in real time and is instantly audit-ready.
Scenario 2: The University Asset Manager

With hundreds of HVAC assets across campus, the asset manager uses Fexa + Trakref to track repairs and compliance. Each system has a digital profile with unique compliance triggers. When a maintenance crew completes a service, the record is tagged, timestamped, and automatically included in Trakref’s compliance reports. The asset status and next steps are clear.
Scenario 3: The Facilities Director at a Retail Chain
Reviewing leak rates and sustainability KPIs across 250+ locations, the facilities director uses data from the integration to identify chronic offenders and align capital planning. Trakref provides leak data and timelines; Fexa ties in labor, vendor performance, and cost. Together, the system helps prioritize retrofits and upgrades for maximum ESG impact.
This Isn’t Just a Better Workflow—It’s a Smarter Business Case
Although I haven’t been at Trakref for nearly two years, I remember exactly how things used to work.
It was normal—expected, even—for service teams to have someone dedicated to transferring data from their internal work order system to the client’s work order system… and then manually enter the same data into Trakref. Three systems. Three entry points. One job.
On the client side, it didn’t stop there.
I often saw internal staff whose full-time job was to check that the data entered by contractors was accurate, consistent, and compliant. They’d review submissions line by line, trying to catch errors, missing fields, and timeline inconsistencies.
That governance process?
- It was subjective.
- It was expensive.
And it was often focused on the wrong things—catching formatting mistakes instead of spotting deeper compliance failures.
The gaps stayed hidden, and the overhead kept growing. This new model eliminates all of that.
And since the API can port or connect data from anywhere it can receive information, it also means this integration could deliver added benefits between Wo systems of both the client and the service provider.
Here’s how teams can expect to see value:
- Fewer manual data entry steps for refrigerant-related work orders
- Reduce the staff needed to manage the existing Business As Usual Approach – the audit trail is now digital and flaggable.
- Reduction in audit prep time thanks to structured, validated, time-stamped records
- Fewer regulatory penalties due to missed inspections or bad refrigerant tracking
- Technician onboarding time was cut in half with guided prompts and pre-tagged asset profiles
When you eliminate triple-entry workflows and replace subjective oversight with embedded logic,
compliance doesn’t just get easier—it gets cheaper, faster, and more accurate.
This is more than software.
It’s a smarter business case for how teams work, how compliance is managed, and how operations scale.
The Pioneering efforts of Trakref and Fexa?
Since 2011, Trakref has been a compliance engine, a purpose-built software system for refrigerant regulations, leak tracking, and environmental performance. For over a decade, it has supported grocers, universities, data centers, and retailers with structured, rule-based workflows designed for environmental compliance and ESG alignment.
Fexa is a next-generation CMMS platform focused on intelligent, scalable work order and facilities management. With deep configurability and powerful integrations, it helps multi-site operators streamline operations, reduce downtime, and manage vendors and assets at scale.
Together, Trakref and Fexa deliver a new kind of facilities management experience: audit-ready, compliance-first, and asset-centric from the ground up. Significant advancements have been achieved within the industry over the past year, emphasizing community efforts, partnerships, and key initiatives in areas such as women in cooling and heating, and sustainability in refrigerant management.
Where Do We Go From Here: AI, Real-World Readiness, and the Road Ahead for a Sustainable Future
At Carbon Connector, this is a milestone for us, too.
It validates the supply chain solutions we’ve been pioneering and builds on the incredible contributions made by our partners in grocery, retail, and the cold chain. We’ve seen firsthand how these tools can transform operations, and now, we’re taking that momentum into the next chapter. Our efforts are driven by the urgent need to combat climate change and create a more sustainable future.
We’re not done. We’re just getting started.
We’re applying these same principles to:
- Asset identification at scale
- Faster, more accurate leak detection
- Workforce predictability and retention
- Outcome-driven strategies that reduce emissions, boost system performance, and deliver measurable cost savings
👁️ Keep your eye on technologies like AKO and Bueno
They represent the next frontier. From managed services to intelligent diagnostics and AFDD integrations, we’re helping usher in a smarter, leaner, more transparent HVAC/R ecosystem.
Better for Teams. Better for Results.
This is a milestone that matters not just for compliance but for people.
For the overworked technician, the data manager juggling spreadsheets, the ESG lead prepping disclosures, and the operator trying to do more with less.
Today, Fexa/Trakref removed a costly key swivel chair.
They’ve embedded the rules.
They’ve made compliance a real-time, low-friction, high-value, achievable outcome
Welcome to the third way.
Congratulations to everyone using—or planning to use—the Trakref + Fexa integration.
Join the conversation! What’s your biggest challenge with compliance in HVAC/R right now?
Discover How Fexa and Trakref are Revolutionizing HVAC/R Compliance
Dive deeper into how the Fexa + Trakref integration creates a proactive, rules-based workflow that eliminates compliance headaches and transforms facilities management.